Have you ever wondered about the meticulous process behind the seemingly simple beakers and test tubes in a laboratory? What are the steps involved in creating these essential tools? How do manufacturers ensure the safety and quality of each piece of lab glassware?
Lab glassware manufacturing is a complex and precise process, involving several critical steps such as raw material processing, molding, cooling, annealing, and rigorous quality control. This process ensures that the glassware meets the high standards required for scientific research and testing.
Let’s delve deeper into each stage of this fascinating process, shedding light on the science behind lab glassware manufacturing.
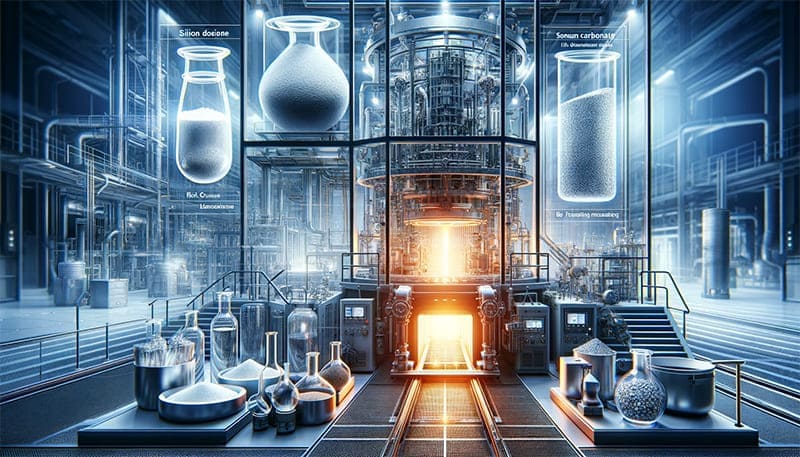
The Journey from Raw Materials to Glass Liquid
The first step in the production of lab glassware is the processing of raw materials. Key ingredients like silicon dioxide, sodium carbonate, and limestone are melted together to form a homogenous glass liquid. This process requires high temperatures and careful monitoring to ensure the correct chemical composition.
Shaping the Future: Molding Techniques in Glassware Production
Once the glass liquid is ready, it is molded into various shapes to create beakers, test tubes, and other lab equipment. Techniques like flow casting, blow molding, extrusion, and rotation molding are employed. Each method has its unique advantages and is chosen based on the desired shape and properties of the final product.
Cooling, Annealing, and Beyond: Ensuring Glassware Integrity
After the glassware is shaped, it undergoes cooling and annealing. This step is crucial for relieving internal stresses and improving the strength and durability of the glass. Additional processes such as deburring and cleaning are also conducted to enhance the quality of the product.
A Close Look: Inspection and Quality Control
The next phase is inspection and quality control. Each piece of glassware is visually inspected and measured for precision. This step ensures that the products not only meet aesthetic standards but also adhere to scientific accuracy.

Delving Deeper: The Significance of Each Manufacturing Step
Understanding the importance of each stage in lab glassware manufacturing reveals the dedication to precision and safety in this field. Let’s explore further:
Raw Material Processing: The Foundation of Quality
The journey begins with the selection and processing of raw materials. The purity and composition of these materials are critical, as they determine the chemical and physical properties of the final glass product. High-quality raw materials lead to glassware that can withstand extreme temperatures and resist chemical corrosion.
Molding: Crafting with Precision
The molding process is where science meets art. Here, the molten glass is transformed into functional shapes. The method chosen—be it blow molding or extrusion—depends on the type of glassware being produced. This step is not just about shaping but also about ensuring uniform thickness and structural integrity.
Cooling and Annealing: Strengthening the Glass
Cooling and annealing might seem passive, but they are anything but. Controlled cooling prevents the formation of stress points, while annealing strengthens the glass. This stage is crucial for ensuring that the glassware can handle thermal shocks and mechanical stress during laboratory use.
Inspection and Packaging: The Final Guardians
Before the glassware reaches the hands of scientists, it undergoes stringent inspection. This is where flaws are detected and quality is assured. Only glassware that passes these tests makes it to packaging, ready to be shipped to laboratories around the world.
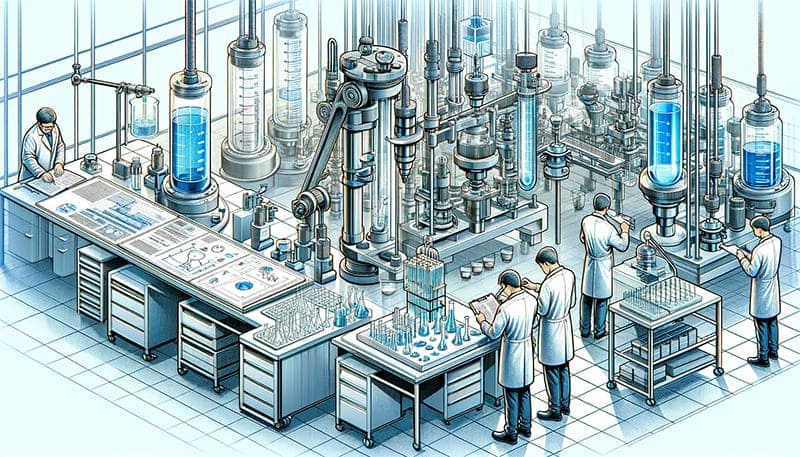
Ensuring Excellence: The Pillars of Quality in Glassware Manufacturing
Quality control is integral to the production of lab glassware. This includes:
- Quality Control of Raw Materials: Strict checks are in place to ensure that the raw materials used are of the highest quality and meet specific chemical requirements.
- Production Technique Control: Advanced production techniques and equipment are utilized, along with strict standard operating procedures, to guarantee the stability and reliability of the products.
- Quality Inspection Control: A comprehensive quality inspection system is established to rigorously test raw materials, semi-finished, and finished products.
- Safety and Environmental Control: Safety protocols and environmental protection measures are strictly followed to ensure a safe and sustainable production process.
After-Sales Service: The Final Step in Customer Satisfaction
Finally, after-sales service plays a crucial role in maintaining customer satisfaction and product reputation. This includes providing detailed product usage instructions, maintenance tips, and efficient complaint handling.
The Role of Quality Controls in Ensuring Excellence
Each quality control measure in the manufacturing process serves as a guardian of excellence:
- Quality Control of Raw Materials: This step ensures that the glass starts on the right foot, chemically sound and pure.
- Production Technique Control: By adhering to advanced production techniques, manufacturers ensure consistent quality and reliability in every batch of glassware.
- Quality Inspection Control: This comprehensive system of checks and balances is what makes laboratory glassware trustworthy for critical scientific work.
- Safety and Environmental Control: These measures reflect the industry’s commitment to not only producing quality glassware but also protecting the environment and the people involved in the manufacturing process.
Beyond the Sale: Ensuring Long-Term Satisfaction
After-sales service is more than just a value-added benefit; it’s a commitment to the customer’s ongoing satisfaction and safety. Effective after-sales support ensures that users can maximize the potential of their lab glassware, understanding its maintenance and optimal usage. It also serves as a feedback loop for manufacturers to continually improve their products.
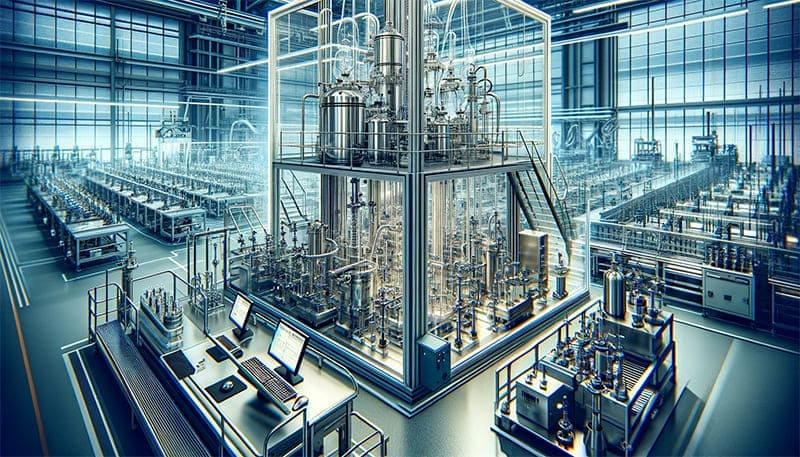
Bridging Science and Practicality: The Importance of Production Technique Control
The production technique control in lab glassware manufacturing is a critical bridge between scientific theory and practical application. It involves:
- Ensuring that the equipment used is state-of-the-art, capable of delivering precision and consistency.
- Adhering to strict standard operating procedures that dictate every minute detail of the production process.
- Implementing a quality management system that oversees every step to guarantee that each piece of glassware meets the necessary standards.
This meticulous attention to production techniques is what allows lab glassware to be reliable under rigorous scientific experimentation.
The Unseen Heroes: Quality Inspection Teams
Quality inspection teams are the unsung heroes in the manufacturing process. These professionals employ various tools and methodologies to evaluate the glassware at multiple stages:
- Raw material inspection ensures that only the best quality materials are used.
- In-process inspection monitors the glassware as it takes shape, identifying and addressing any issues immediately.
- Final product inspection is the last line of defense, ensuring that only flawless products reach the customer.
This multilayered inspection process is essential for maintaining the high standards expected in laboratory settings.
Safety and Environment: A Dual Focus
In today’s world, manufacturing processes are not just about the end product but also about how they impact both people and the planet. Safety and environmental controls in lab glassware manufacturing include:
- Implementing safety protocols to protect workers from the hazards of handling and processing glass at high temperatures.
- Installing waste gas treatment facilities and other measures to minimize the environmental impact of the manufacturing process.
- Complying with global and local environmental regulations, reflecting a commitment to sustainable manufacturing practices.

After-Sales Service: Completing the Customer Experience
The role of after-sales service in lab glassware manufacturing extends beyond mere customer satisfaction. It encompasses:
- Providing detailed usage instructions, which is crucial for the safe and effective use of the glassware.
- Offering maintenance advice to prolong the life of the products.
- Handling customer complaints and feedback, which is vital for continuous improvement in both product and process.
In Summary: A Symphony of Science and Care
The manufacturing of laboratory glassware is a symphony of science, precision, and care. Each step, from the selection of raw materials to after-sales service, plays a critical role in delivering products that are not just tools, but partners in the scientific quest for knowledge. This process is a testament to the commitment of manufacturers to quality, safety, and environmental stewardship. It’s a world where science meets responsibility, resulting in products that scientists trust and rely on in their daily quest to unravel the mysteries of the world around us.
As we have traversed through each step of this intricate process, from the careful selection of raw materials to the meticulous quality control measures, it’s clear that every piece of glassware in a laboratory is a product of dedicated craftsmanship and scientific precision.
But this journey doesn’t just end here. It extends into the laboratories where these glass tools play a pivotal role in groundbreaking research and discoveries. As you look at a piece of lab glassware, remember the symphony of processes it has gone through and the expertise involved in its creation. Let this knowledge inspire a greater appreciation for the tools that aid in unlocking the mysteries of science.
So, next time you hold a beaker or a test tube, think of the hands that crafted it, the minds that engineered it, and the commitment to quality and safety that ensured its place in your hands. And most importantly, consider how your work in the lab contributes to this ongoing cycle of discovery and innovation.
Together, let’s continue to celebrate and support the meticulous craft of lab glassware manufacturing—a field where science meets precision, creating tools that not only serve our current needs but also pave the way for future scientific breakthroughs.