Have you ever wondered how your laboratory glassware stands up to the harsh conditions it’s subjected to daily? Or perhaps, why some glassware lasts longer and performs better than others in extreme environments? These questions are vital, especially when the integrity of scientific research hinges on the reliability of the glassware used.
Testing the limits of glassware through environmental adaptability tests is essential in ensuring the safety, durability, and reliability of these vital tools in laboratories. This process involves rigorous assessments under varying conditions to ascertain how well glassware can withstand temperature changes, pressure variations, chemical exposure, and more.
Maintaining a keen interest in this topic can revolutionize your understanding and usage of laboratory glassware.
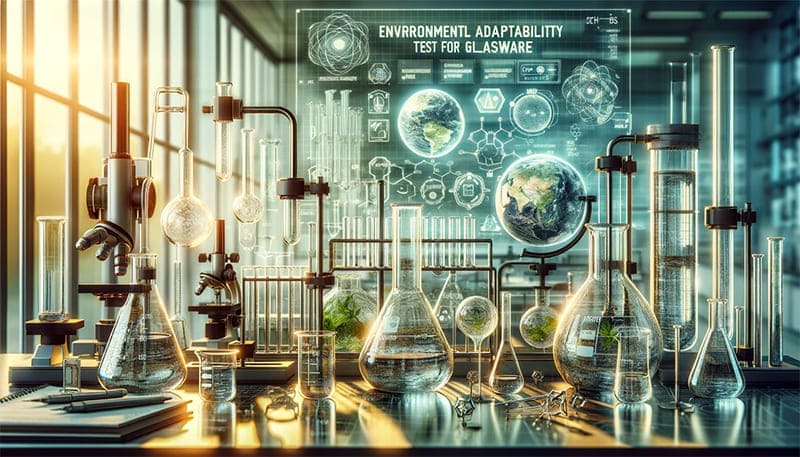
What are Environmental Adaptability Tests for Glassware
Environmental adaptability tests for glassware are designed to simulate the different conditions the glassware will encounter in real-world laboratory settings. This includes temperature fluctuations, mechanical stress, chemical reactions, and pressure changes. The primary purpose is to ensure that the glassware maintains its integrity, functionality, and safety under various conditions. By understanding the limitations and capabilities of glassware, laboratories can prevent accidents, contamination, and equipment failure, ensuring smoother and safer operations.
Why Conduct Environmental Adaptability Tests?
Conducting these tests is crucial for several reasons:
- Safety: Ensuring that glassware doesn’t crack, shatter, or fail when subjected to extreme conditions is vital for the safety of laboratory personnel.
- Quality Control: Regular testing helps maintain high quality and performance standards for laboratory glassware.
- Cost-Efficiency: By identifying and addressing potential failures early, laboratories can save on the cost of replacing damaged equipment.
- Regulatory Compliance: Many industries are governed by strict regulations that require evidence of environmental adaptability testing.
How are These Tests Conducted?
Conducting environmental adaptability testing for glass instruments is crucial to evaluate their performance and safety under various conditions. Here’s a guide to performing these tests:
- Define Test Scope and Conditions: Before beginning, specify the scope and conditions of the test, including temperature, humidity, pressure, light exposure, duration, and sample quantity.
- Select Test Samples: Choose representative glass instruments to assess their performance under different conditions. The samples should represent the type of glass, manufacturing materials, techniques, and specifications.
- Prepare Testing Equipment: Based on the test conditions, prepare the necessary equipment like temperature and humidity controllers, and pressure testing apparatus. These should offer precise environmental control to simulate various real-life conditions.
- Set Up Testing Procedures: Establish a testing program according to the defined scope and conditions, including heating, cooling, humidifying, dehumidifying, and pressure variations. Monitor the sample changes closely during the test and record all pertinent data.
- Analyze Test Data: Evaluate the performance and safety of the glass instruments based on the test data. Assessments might include strength, durability, chemical compatibility, cleanliness, and seal integrity.
- Evaluate Environmental Adaptability: Rate the instruments’ environmental adaptability from the analysis. If the samples show good performance and safety in simulated conditions, they are deemed adaptable; otherwise, improvements may be necessary.
What Comes After Testing?
After the tests are conducted, it’s important to:
- Formulate Improvement Measures: Based on the evaluation, develop measures to address any issues with the environmental adaptability of the instruments. This could include changes in materials, manufacturing techniques, or structural design optimizations.
- Verify Improvement Measures: After implementing improvements, verify their effectiveness and feasibility, possibly through additional adaptability testing.
- Establish Test Records: Document the entire testing process and results, creating detailed records. This documentation is vital for tracking and managing the performance and safety of the glass instruments and serves as a reference for future research and improvements.
- Regular Review and Maintenance: Even after glass instruments pass environmental adaptability tests and are in use, regular reviews and maintenance are essential. This helps identify and address potential issues or safety hazards, ensuring laboratory safety and reliability.
Environmental adaptability testing for glass instruments requires meticulous design, operation, data analysis, and evaluation. Such testing provides a comprehensive understanding of the instruments’ performance and safety levels under various conditions, ensuring laboratory safety and integrity.
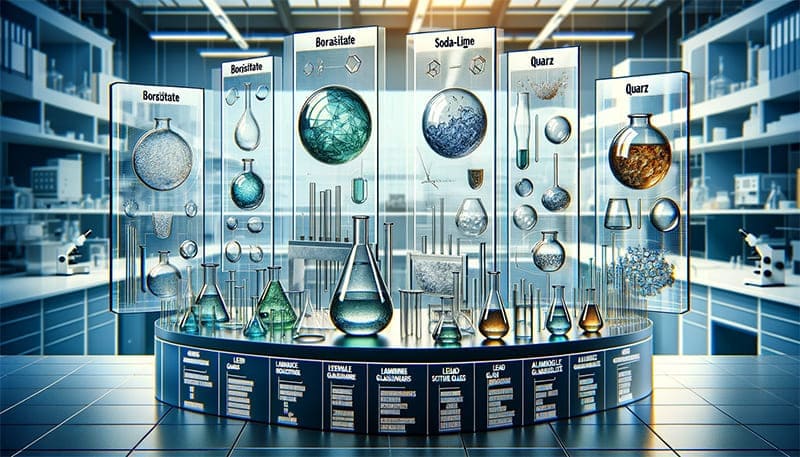
Comparative Analysis of Laboratory Glassware Materials
When selecting glassware for laboratory use, understanding the properties and limitations of different glass materials is crucial. The adaptability of glassware to environmental conditions can significantly impact its performance and safety in the laboratory. The following table compares various glass materials used in laboratory glassware, detailing their endurance limits, specific considerations, and precautions necessary for their use.
Glass Material | Endurance Limits | Commentary | Precautions |
---|---|---|---|
Borosilicate Glass | High thermal resistance, low expansion | Preferred for high-temperature applications due to excellent thermal shock resistance | Avoid sudden, extreme temperature changes |
Soda-Lime Glass | Moderate thermal resistance, higher expansion | Common and economical, but more prone to thermal shock | Gradual heating and cooling recommended |
Lead Glass | High density, radiation shielding properties | Used for storing and viewing radioactive samples | Handle with care due to potential lead content |
Quartz Glass | Very high temperature resistance, UV transparency | Ideal for UV applications and extreme temperatures | Expensive and requires careful handling |
Aluminosilicate Glass | Very high strength and thermal resistance | Used in demanding applications, resistant to scratches and thermal shock | Ensure compatibility with specific chemicals |
Selecting the right type of glass for your laboratory equipment is not just a matter of preference but of safety and efficiency. The table above provides a snapshot of how different materials perform under stress and what to consider when choosing them. It’s essential to match the glassware with the intended use and conditions to ensure optimal performance and safety.
As we continue to push the boundaries of scientific research, the glassware we use must not only keep up with our demands but also ensure the integrity and safety of our experiments. Understanding the properties and limits of different glass materials is a step towards more informed decisions in laboratory settings.
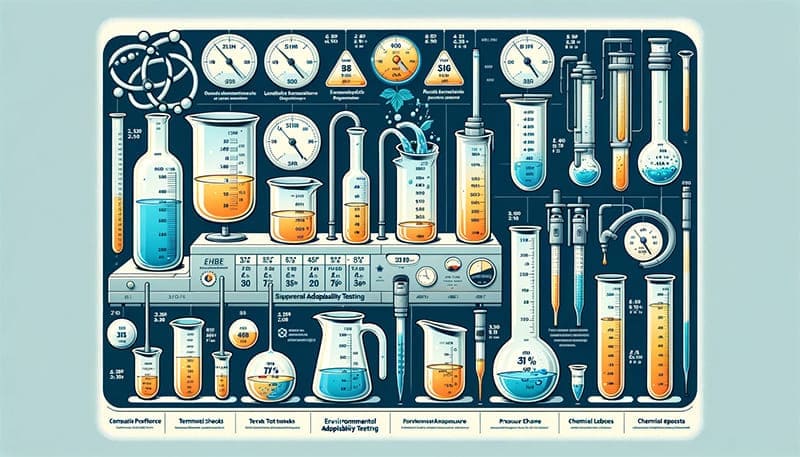
Comparative Performance of Laboratory Glassware in Environmental Adaptability Testing
When it comes to ensuring the safety and reliability of laboratory operations, understanding how different types of glassware respond to environmental adaptability tests is crucial. This section will delve into the performance of various laboratory glass instruments under such testing. The table below outlines the types of glassware, the key tests they are subjected to, the minimum property requirements, their endurance limits, and specific precautions that should be taken during use.
Name | Key Focus of Tests | Minimum Property Requirements | Endurance Limits | Precautions |
---|---|---|---|---|
Beakers | Thermal shock, chemical resistance | Must withstand routine heating and cooling, resist common chemicals | High resistance to heat and moderate chemical stress | Avoid extreme, rapid temperature changes |
Flasks (Erlenmeyer, Volumetric) | Thermal shock, pressure changes, chemical resistance | Resilient to pressure, temperature variations, and chemical exposure | High thermal resistance and moderate pressure resistance | Gradual changes in temperature and pressure recommended |
Test Tubes | Chemical resistance, heat tolerance | Durable against a wide range of chemicals, withstand moderate heating | Moderate to high thermal and chemical resistance | Use in appropriate test tube holders; even heating |
Pipettes | Precision, chemical resistance | Accurate volume delivery, resistant to chemicals | Resistant to chemical wear, maintain calibration | Avoid mechanical stress and extreme temperatures |
Burettes | Precision, chemical resistance | Accurate volume control, chemical durability | High precision under repeated use, chemical resilience | Regular calibration and careful cleaning |
Petri Dishes | Chemical and biological resistance | Resist biological contamination, chemical neutral | Moderate chemical resistance, high biological neutrality | Sterilize thoroughly, handle with care |
Understanding the various adaptability tests and performance metrics for laboratory glassware is not just about meeting standards, but about ensuring the highest level of safety and efficiency in scientific work. The table above provides a snapshot of the endurance and limitations of commonly used glassware, guiding users in selecting the right type for their specific needs.
Whether it’s conducting a simple experiment or a complex research study, choosing the right glassware is essential. Knowing the specific endurance limits, property requirements, and necessary precautions for each type helps maintain a safe and efficient laboratory environment. Always refer to manufacturer guidelines and industry standards when selecting and using laboratory glassware to ensure optimal performance and safety.
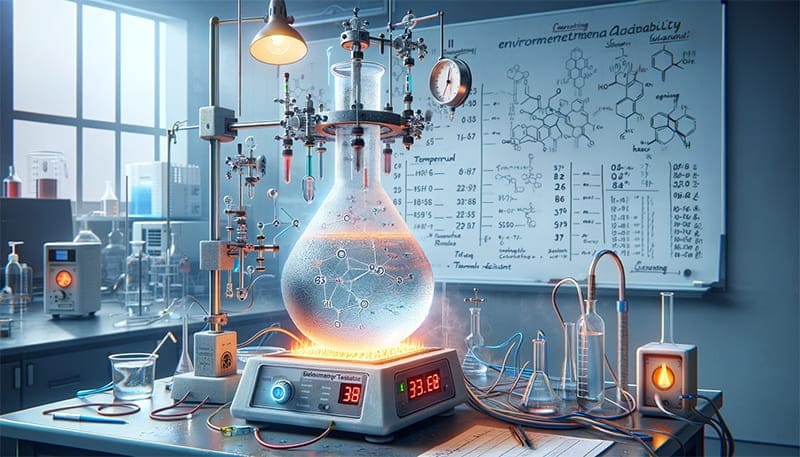
Conducting Environmental Adaptability Tests on Erlenmeyer Flasks
Before diving into the specific procedures for testing the adaptability of an Erlenmeyer flask to various environmental conditions, it’s essential to understand the importance of these tests and how they contribute to maintaining laboratory safety and integrity. These tests ensure that the glassware can withstand typical laboratory conditions such as rapid temperature changes, exposure to chemicals, and physical stress. Now, let’s look at how to carry out these crucial tests step by step.
Preparation:
- Select the Flask: Choose a standard Erlenmeyer flask that is commonly used in your laboratory setting. Ensure it’s new or in like-new condition to avoid pre-existing stress influencing the results.
- Define the Testing Parameters: Establish the range of temperatures, pressures, and chemicals that the flask is likely to encounter during normal use. For example, temperature ranges might include anything from freezing point to the boiling point of common solvents.
- Prepare the Testing Equipment: Set up equipment for temperature control (like water baths or ovens), pressure application (like vacuum pumps), and chemical exposure (containers with acids, bases, solvents, etc.).
Testing Procedures:
- Thermal Shock Resistance:
- Gradually heat the flask to the maximum expected temperature and then quickly immerse it in a cold environment, such as an ice-water bath.
- Inspect the flask for any signs of cracking or breakage.
- Repeat the process several times to simulate repeated use.
- Chemical Durability:
- Fill the flask with a series of chemical reagents it’s likely to encounter, starting with water, moving to mild solvents, and then to more aggressive acids or bases.
- After exposure to each chemical for a predetermined duration, inspect the glass for etching, discoloration, or any other signs of chemical degradation.
- Mechanical Strength:
- Perform a drop test from a standard height or apply a standard weight or force to the flask to simulate accidental impacts or pressures.
- Check for any cracks, chips, or breakages that occur as a result of the mechanical stress.
Data Collection and Analysis:
- Documentation: Record all conditions and observations meticulously, including the temperature ranges, chemicals used, duration of exposure, and any signs of wear, degradation, or failure.
- Analysis: Evaluate the severity and type of damage or change in the flask’s condition. Compare these findings against the manufacturer’s specifications and industry standards for similar types of glassware.
Post-Test Procedures:
- Clean and Dispose: Properly clean the flask if it passes the tests and is deemed safe to reuse, or dispose of it following safety guidelines if it’s damaged.
- Review and Adjust Testing Protocol: Based on the outcomes, consider whether the test conditions accurately reflect the real-life conditions the flask will face. Adjust future tests accordingly.
- Report Findings: Compile the data, analysis, and any recommendations into a report for laboratory personnel, safety officers, or other relevant parties.
By following these steps, you’ll be able to determine the Erlenmeyer flask’s adaptability to environmental conditions and make informed decisions about its use, maintenance, and replacement in your laboratory setting. This process not only ensures the safety and efficiency of your operations but also contributes to the overall reliability of the scientific work conducted in your facility.
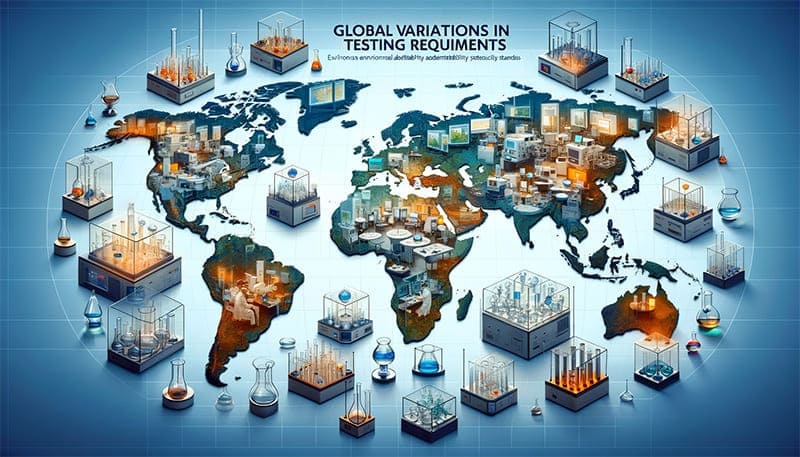
Global Variations in Testing Requirements
Understanding the global landscape of testing requirements is crucial for laboratories and manufacturers that operate internationally or handle equipment from various parts of the world. Different countries and regions may have unique standards and regulations governing the environmental adaptability testing of laboratory glassware. These variations can significantly affect how glassware is produced, tested, and certified before it reaches a laboratory.
In the European Union, for example, glassware might need to adhere to specific ISO standards that dictate the quality and safety of laboratory materials, including detailed protocols for thermal resistance and chemical durability. Meanwhile, in the United States, standards set by the American Society for Testing and Materials (ASTM) might take precedence, providing a different set of guidelines and test methods.
Asian countries may have their own set of standards or may adopt international ones, with variations tailored to regional needs or specific industries. It is not uncommon for countries to have a hybrid approach, blending international standards with local regulations to address specific environmental factors or industrial practices prevalent in that region.
Manufacturers and laboratories deal with these variations through a combination of strategies:
- Compliance with International Standards: Many opt to comply with widely recognized international standards like ISO or ASTM, ensuring a broad acceptance of their products and practices.
- Regional Certifications: Obtaining certifications specific to key markets allows manufacturers to meet the local regulatory requirements and build trust with regional customers.
- Versatile Production Lines: Some manufacturers design their glassware to meet the highest common denominator among various standards, ensuring their products are over-qualified rather than under-qualified for most markets.
- Continuous Monitoring and Adaptation: Regulatory landscapes can change, necessitating ongoing monitoring of changes in standards and tests in different countries. Manufacturers and laboratories often have dedicated teams or hire consultants to stay updated and adapt accordingly.
- Collaboration and Communication: Engaging in dialogue with standard-setting bodies and industry groups helps manufacturers and laboratories anticipate changes and influence the development of standards that reflect technological advancements and safety research.
By navigating these global variations, manufacturers and laboratories ensure that their glassware is not only compliant with local regulations but also meets the highest standards of safety and performance, regardless of where it is used. Understanding and addressing these global differences is key to maintaining the integrity and reliability of laboratory operations worldwide.
Conclusion
As we continue to push the frontiers of science, the integrity and safety of our laboratory tools are paramount. Understanding and implementing rigorous environmental adaptability tests for glassware is not just a matter of regulatory compliance; it is a commitment to excellence and safety in scientific research. Let us take this knowledge forward, advocate for the highest standards in our laboratories, and continuously strive for improvements that enhance the reliability and safety of our scientific explorations. Engage, innovate, and inspire safer practices for a better tomorrow in research.