Are you tired of the constant struggle to reduce costs and waste in your glassware manufacturing processes? Do you find yourself wondering how to make your production leaner and greener without compromising quality? You are not alone. Many manufacturers are on the quest to find the perfect balance between efficiency, cost, and environmental responsibility.
In today’s competitive market, reducing production costs and material waste in glassware manufacturing is not just a financial necessity; it’s an environmental imperative. By adopting lean and green strategies, businesses can minimize waste, reduce costs, and improve their overall sustainability. This not only benefits the bottom line but also contributes to a healthier planet.
Keep reading to discover how you can implement these strategies in your manufacturing processes.

Understanding Lean and Green Manufacturing
What is “Lean and Green”?
Lean manufacturing is a systematic approach to minimize waste without sacrificing productivity. It involves continuous improvement practices, optimizing processes, and eliminating inefficiencies. Green manufacturing, on the other hand, focuses on reducing environmental impact through sustainable practices, recycling, and waste management. When combined, lean and green manufacturing create a powerful strategy for businesses to become more efficient and eco-friendly.
Why is Lean and Green Important in Glassware Manufacturing?
Glassware manufacturing involves various resource-intensive processes, from melting and molding to cooling and finishing. Each stage offers opportunities for cost-saving and waste reduction. By implementing lean and green practices, manufacturers can:
- Reduce energy consumption and costs.
- Minimize raw material usage and waste.
- Improve product quality and consistency.
- Enhance compliance with environmental regulations.
- Boost reputation and customer satisfaction.
The Imperative of Lean and Green in Glassware Manufacturing
The glassware manufacturing industry is inherently resource-intensive, involving high energy consumption and substantial raw material use in melting, molding, and finishing processes. This intensity presents a compelling case for the imperative of Lean and Green practices. Adopting these methods offers significant opportunities for cost savings through more efficient use of materials and energy. Waste reduction is not only a matter of cost but also of environmental stewardship, as minimizing waste contributes to less landfill use and reduced environmental impact. Additionally, by enhancing energy efficiency and adhering to stricter environmental regulations, manufacturers can not only reduce their ecological footprint but also achieve compliance with evolving legal standards, avoiding penalties and bolstering their market reputation. In essence, Lean and Green strategies are not just beneficial; they are essential for the sustainable, profitable, and responsible operation of glassware manufacturing facilities.
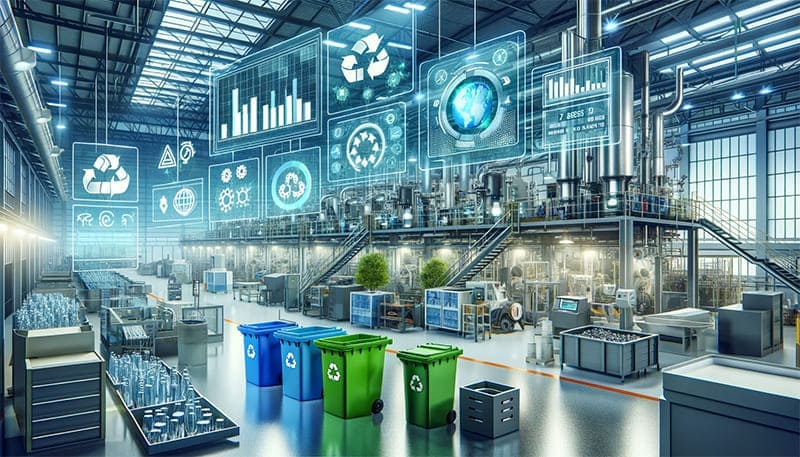
Strategies for Reducing Production Costs and Material Waste
1. Optimize Design and Materials
- Design for Efficiency: Simplify designs to reduce material usage and manufacturing steps. Consider the entire lifecycle of the product, from production to disposal.
- Material Selection: Use recycled or sustainable materials where possible. High-quality materials might have a higher upfront cost but can reduce waste and improve the durability of the final product.
2. Advanced Processing Techniques
- Precision Manufacturing: Invest in advanced technologies like precision cutting and automated assembly to reduce errors and material wastage.
- Process Optimization: Continually review and refine manufacturing processes to improve yield and reduce defects.
3. Scale Production Smartly
- Batch Size Optimization: Adjust batch sizes to meet demand without overproducing. This reduces the risk of excess inventory and waste.
- Efficient Layout and Flow: Design your workspace for maximum efficiency, reducing movement and wait times between processes.
4. Embrace Recycling and Reuse
- Recycle Scrap: Implement systems to collect and recycle glass scraps and defective products.
- Reuse in Production: Find ways to reuse materials in the manufacturing process, such as using cullet (recycled broken or waste glass) in glass production.
5. Implement Advanced Production Technologies
- Automation and Robotics: Automate repetitive tasks to improve precision and reduce waste. Robotics can handle dangerous or complex tasks with consistency.
- Energy-Efficient Equipment: Invest in modern equipment that uses less energy and resources while maintaining or improving productivity.
6. Strengthen Production Management
- Lean Six Sigma: Adopt Lean Six Sigma methodologies to identify and eliminate waste and defects in your processes.
- Inventory Management: Use just-in-time inventory systems to reduce storage costs and waste associated with unsold stock.

Building and Maintaining a Lean and Green Culture
7. Enhance Skills and Quality Awareness
- Staff Training: Regularly train staff on new techniques and the importance of waste reduction. Skilled workers are more efficient and make fewer mistakes.
- Quality Control: Implement strict quality control measures at every stage to ensure defects are caught early and don’t lead to waste.
8. Continuous Innovation and Research
- Invest in R&D: Keep up with the latest advancements in materials and manufacturing technologies. Innovation can lead to more efficient, less wasteful production methods.
- Sustainability Goals: Set and strive for clear, measurable sustainability goals to guide your lean and green initiatives.
9. Encourage Employee Involvement
- Idea Sharing: Create a culture where employees are encouraged to suggest improvements. This can lead to innovative ways to reduce waste and improve efficiency.
- Reward Systems: Implement reward systems for ideas that significantly reduce costs or waste, fostering a sense of ownership and pride in the process.
10. Monitor, Measure, and Manage
- Key Performance Indicators (KPIs): Establish KPIs related to waste reduction, energy use, and cost savings. Regularly review these metrics to assess progress and identify areas for improvement.
- Continuous Assessment: Conduct regular audits and assessments of processes to ensure they remain efficient and effective.
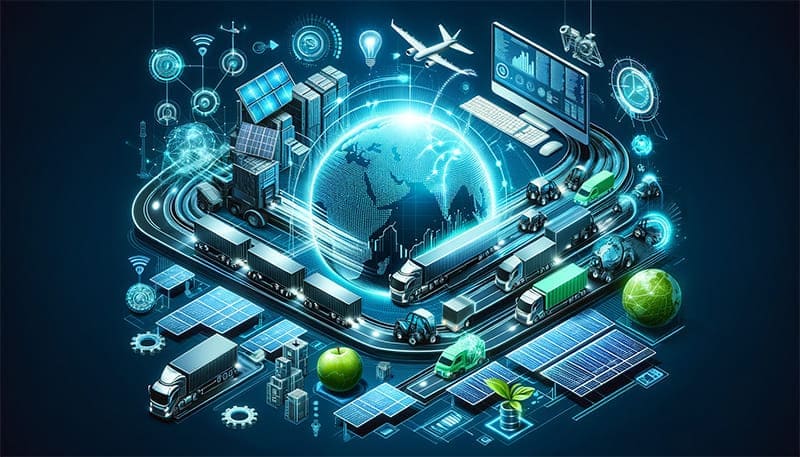
Enhancing Supply Chain Efficiency
11. Partner with Eco-Friendly Suppliers
- Sustainable Sourcing: Choose suppliers who prioritize sustainability in their operations. This includes those who supply recycled materials, use renewable energy, or have efficient logistics.
- Collaborative Planning: Work closely with suppliers to forecast demand accurately, reducing overproduction and excess inventory.
12. Streamline Distribution
- Optimized Routing: Ensure that products are delivered using the most efficient routes and methods. Consider the environmental impact of transportation and look for ways to reduce it.
- Packaging Reduction: Minimize packaging or use recycled or biodegradable materials. Efficient packaging reduces waste and transportation costs.
Utilizing Regulatory Compliance as an Advantage
13. Stay Ahead of Regulations
- Proactive Compliance: Keep abreast of environmental regulations and standards. By exceeding these standards, you can avoid fines and position your company as an industry leader in sustainability.
- Certifications: Obtain certifications like ISO 14001 for environmental management systems. These not only ensure compliance but also demonstrate your commitment to sustainability to customers and stakeholders.
Leveraging Technology for Better Results
14. Invest in Data Analytics
- Predictive Maintenance: Use data analytics to predict when equipment needs maintenance, reducing downtime and waste caused by machine breakdowns.
- Efficiency Insights: Analyze data to identify patterns and inefficiencies in production. This can lead to targeted improvements and innovations.
15. Explore New Technologies
- 3D Printing: Consider using 3D printing for prototyping or producing complex parts. This can reduce waste from traditional manufacturing methods and speed up development.
- Renewable Energy: Invest in renewable energy sources like solar or wind power for your manufacturing facilities. This reduces your carbon footprint and can lead to long-term cost savings.
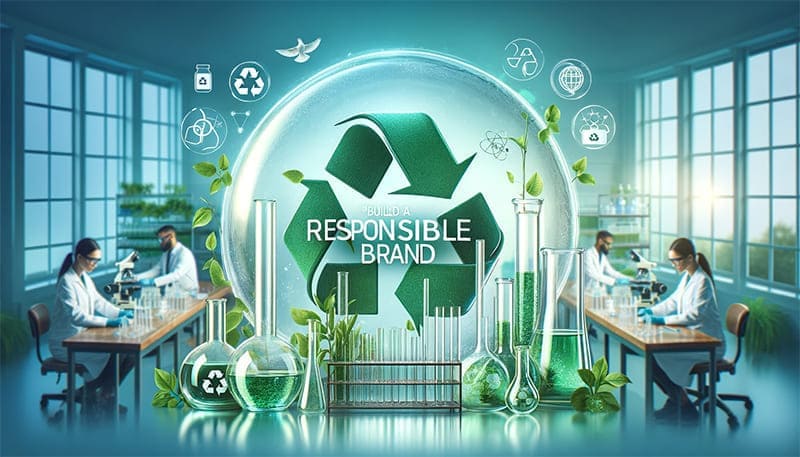
Building a Responsible Brand
16. Communicate Your Efforts
- Transparency: Be open about your sustainability efforts and progress. This builds trust with customers and can enhance your brand’s reputation.
- Marketing: Use your lean and green initiatives as a selling point. Consumers are increasingly looking for products that are environmentally friendly.
Embracing the Circular Economy
17. Implement Circular Economy Principles
- Product Life Extension: Design glassware that is durable and easy to repair, extending its life cycle and reducing the need for new materials.
- Resource Recovery: Establish systems for taking back used products for refurbishing, repurposing, or recycling.
18. Engage in Closed-Loop Recycling
- Local Looping: Collaborate with local recyclers to ensure glass waste is collected, melted, and reused in your own production line, minimizing transportation and raw material costs.
- Quality Control in Recycling: Maintain high standards in the recycling process to ensure that the recycled glass is of sufficient quality to be used in new products.
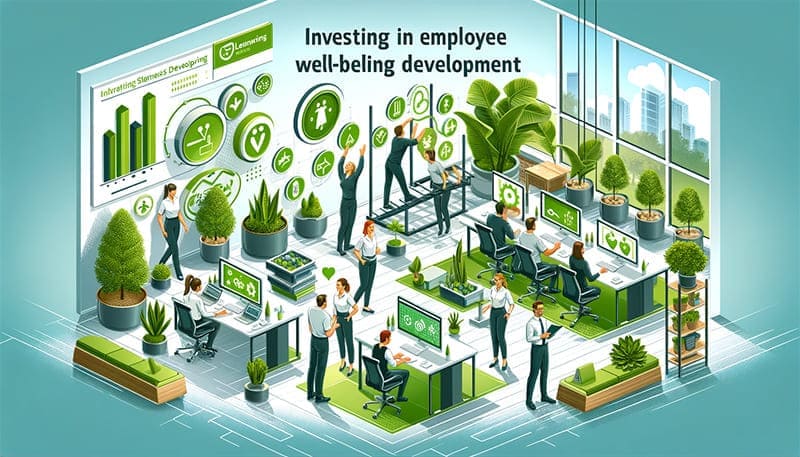
Investing in Employee Well-being and Development
19. Foster a Safe and Healthy Work Environment
- Ergonomics and Safety: Invest in ergonomic tools and machinery, and implement strict safety protocols to prevent workplace accidents and injuries.
- Health and Well-being Programs: Offer programs that support employee health and well-being, such as stress management workshops or fitness memberships.
20. Provide Ongoing Training and Education
- Skill Development: Offer regular training in new technologies, techniques, and sustainability practices, ensuring that employees are up-to-date and proficient.
- Leadership and Development Programs: Develop future leaders from within by providing leadership training and mentorship programs.
Leveraging Partnerships and Collaborations
21. Collaborate for Innovation
- Industry Partnerships: Work with universities, research institutions, and other companies to develop new, sustainable technologies and processes.
- Supplier Collaboration: Engage with suppliers to create more sustainable supply chains and to innovate in materials and logistics.
22. Participate in Industry Consortia
- Standards Development: Join or form consortia aimed at developing industry standards for sustainability, which can help shape regulations and market expectations.
- Shared Learning: Participate in forums and workshops to share and learn best practices in lean and green manufacturing.

Adapting to Market Changes and Consumer Demands
23. Understand and Anticipate Consumer Trends
- Market Research: Regularly conduct research to understand consumer preferences, especially around sustainability and ethics.
- Product Innovation: Use insights from market research to innovate in product design, offering products that meet the latest consumer demands for sustainability and functionality.
24. Respond to Changes with Agility
- Flexible Production Lines: Ensure that your production processes are adaptable, allowing you to quickly respond to changes in demand or to introduce new products.
- Dynamic Business Strategies: Regularly review and adjust your business strategies to take advantage of new market opportunities or to respond to challenges.
Conclusion
Embark on a transformative journey towards sustainability and efficiency in your glassware manufacturing. Embrace the lean and green principles detailed in this comprehensive guide, reducing costs and environmental impact. Let’s innovate, optimize, and lead the way to a more sustainable future. It’s time to act, innovate, and revolutionize your production processes – for the health of your business and our planet. Join the movement today and make a lasting impact! For more insights and resources on lean and green manufacturing, visit Winson and explore a world of sustainable glassware solutions. Together, let’s shape a greener future!