Have you ever pondered the journey of a simple beaker from a molten blob of glass to a vessel holding the future of scientific discovery? This journey is underpinned by a relentless pursuit of perfection in the world of laboratory glassware manufacturing. Here, even the smallest imperfection is not just a defect; it could be the difference between a scientific breakthrough and a failed experiment.
In the quest for ‘Crafting Perfection,’ the key quality control measures in lab glassware manufacturing are both fascinating and stringent. These processes are not just about forming glass; they are about shaping the future of scientific integrity and reliability.
Let’s delve into this unseen yet crucial world, where precision is not just a goal, but a mandatory standard.

Adhering to Regulatory Standards: A Key Pillar in Lab Glassware Manufacturing
Compliance with international and national regulatory standards is paramount in the manufacturing of laboratory glassware. This compliance encompasses adherence to a range of standards and regulations, including but not limited to ISO standards and FDA regulations. These standards are critical in ensuring that the lab glassware produced meets the highest levels of quality and safety.
To ensure ongoing compliance, regular audits and certifications are a necessity. These processes help in maintaining a consistent standard of quality across all products. By adhering to these rigorous standards, manufacturers can assure their clients of the safety and reliability of their products. This adherence is not just a legal obligation, but also a mark of commitment to excellence in the field of lab glassware manufacturing.
Incorporating these elements of regulatory compliance into the manufacturing process plays a significant role in building trust with customers. It assures them that the products they are using in their scientific endeavors are not only effective but also safe and compliant with the highest international standards. This commitment to maintaining regulatory standards underscores the dedication of the lab glassware industry to quality, safety, and continuous improvement.
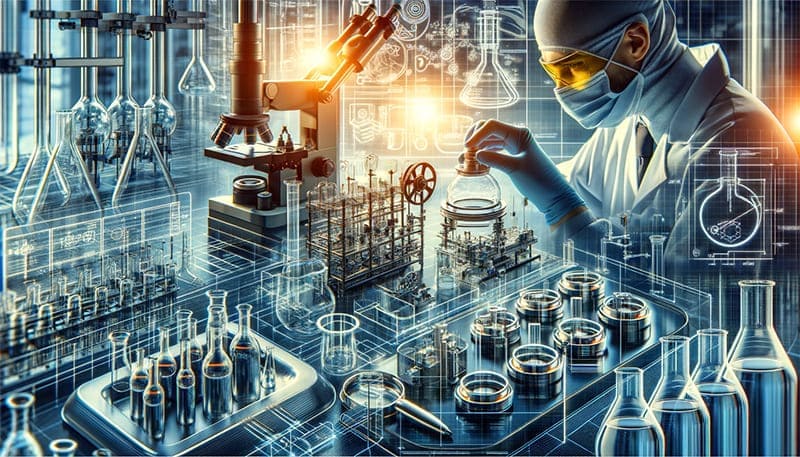
Implementing Stringent Quality Control in Laboratory Glassware Manufacturing
In the realm of laboratory glassware manufacturing, stringent quality control measures are critical to ensure the products meet the highest standards of quality and performance. This essential guide outlines the key steps involved in this process:
1. Rigorous Raw Material Selection: The journey of creating laboratory glassware begins with the careful selection of raw materials, such as silica sand, soda, and limestone. The quality of these materials is pivotal, as it directly influences the overall quality and functionality of the finished glassware. Manufacturers must maintain strict control over the sourcing of these materials, ensuring their reliability. Each batch of raw materials undergoes thorough quality assessments to verify that their chemical composition and physical properties align with stringent standards.
2. Precise Melting and Molding: The core processes of melting and molding the glassware are governed by critical parameters including temperature, duration, and atmospheric conditions. Manufacturers are tasked with meticulously overseeing these processes, guaranteeing adherence to established standards. Moreover, every batch of glassware is subjected to detailed quality inspections to confirm that the shape, size, and surface texture meet specified requirements.
3. Controlled Heat Treatment: To enhance the glassware’s durability and clarity, a crucial heat treatment phase is incorporated. This stage involves carefully calibrated temperature settings, specific durations, and controlled cooling rates. These factors are crucial in determining the glass’s final quality, encompassing aspects like thermal stability, heat resistance, and transparency. Each batch is rigorously tested to ensure these parameters are met.
4. Comprehensive Inspection and Testing: Ensuring the glassware’s compliance with required standards involves a series of inspections and tests. This includes evaluating the appearance, measuring dimensions, conducting pressure tests, and performing leak tests. These procedures are aligned with relevant standards and specifications to maintain accuracy and reliability. Each production batch is methodically examined to affirm compliance with the set quality standards and technical specifications.
5. Environmental Quality Assurance: The manufacturing environment plays a significant role in the quality of the glassware. Factors like air humidity, temperature, dust levels, and microbial presence can impact product quality. Manufacturers, therefore, exert stringent control over the production environment, ensuring it meets the necessary environmental and sanitary guidelines. Regular quality tests are performed on each batch to verify adherence to these environmental and quality standards.
Through these meticulous quality control measures, laboratory glassware manufacturers ensure their products consistently meet the rigorous demands of scientific research, maintaining the highest standards of accuracy, durability, and reliability.
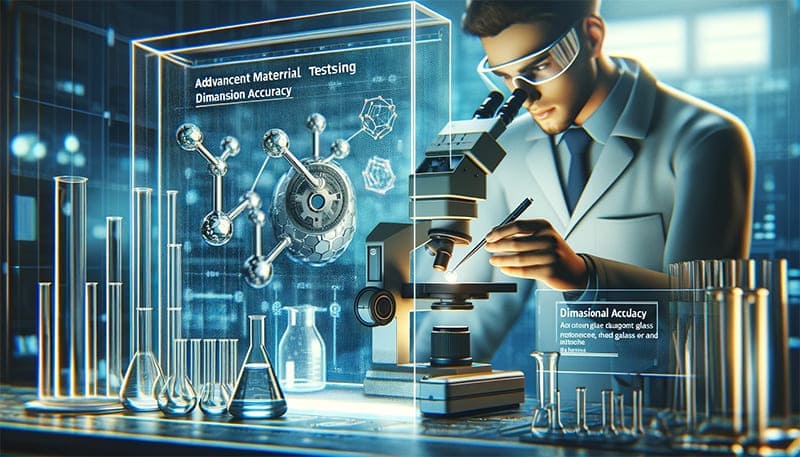
Enhancing Lab Glassware Precision: Advanced Material Testing and Dimensional Accuracy
The manufacturing of laboratory glassware hinges on two pivotal elements: advanced material testing and dimensional accuracy. These steps are critical in fabricating glassware that meets the rigorous demands of scientific research. Advanced material testing scrutinizes the glass at a molecular level for utmost resilience, while precision in dimensional accuracy is essential for the reliability of volumetric measurements in experiments.
6. Advanced Material Testing: Beyond the selection of high-quality raw materials, the implementation of advanced testing methods is crucial. This involves conducting detailed analyses of glass properties such as resistance to chemical corrosion, thermal shock, and mechanical stress. Techniques like spectroscopy and microscopy are employed to examine the glass at a molecular level, ensuring the materials used can withstand the stringent requirements of laboratory use.
7. Precision in Dimensional Accuracy: Dimensional accuracy is paramount for laboratory glassware, especially for volumetric instruments. Precision engineering and the use of state-of-the-art measurement tools are employed to ensure that each piece of glassware conforms to exact volume and dimension specifications. This level of precision is essential for ensuring accurate measurements in scientific experiments.
In sum, the integration of meticulous material testing and precise dimensional control is foundational in lab glassware manufacturing. This approach not only ensures the robustness and suitability of glassware for lab use but also upholds the accuracy vital for scientific integrity, making it indispensable in the realm of scientific discovery.
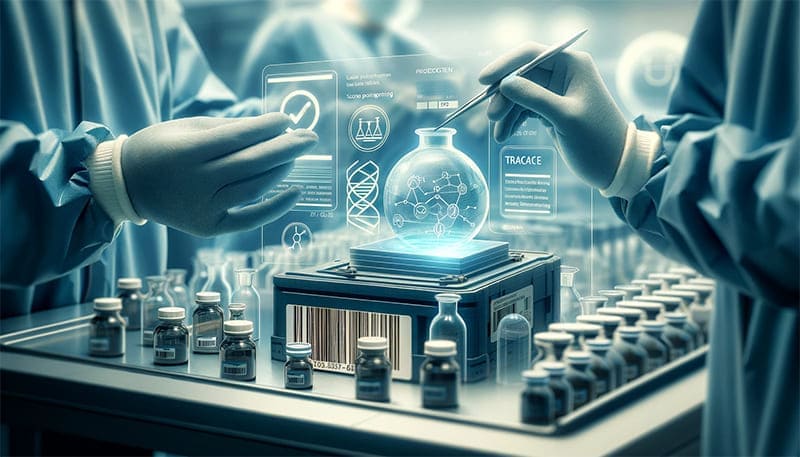
Ensuring Integrity and Safety in Lab Glassware Manufacturing: Traceability and Packaging
A critical aspect of producing high-quality laboratory glassware lies in the meticulous attention to traceability and secure packaging. This approach is essential not only for maintaining quality but also for ensuring the safety and integrity of the products throughout their lifecycle.
8. Traceability and Documentation: Maintaining detailed records and traceability for each product batch is crucial. This includes documentation on the origins of raw materials, the production process, quality control checks, and distribution. Traceability ensures that if any quality issues arise, they can be swiftly traced back to their source, allowing for prompt corrective measures.
9. Packaging and Storage: The final stage in the manufacturing process involves appropriate packaging and storage, a step critical in protecting the glassware from damage and contamination during transit and storage. Using packaging materials that maintain the integrity and cleanliness of the glassware until it reaches the end-user is essential. This ensures that the products are not only delivered in perfect condition but also remain safe for use in various laboratory applications.
In summary, the integration of robust traceability systems and careful packaging and storage practices is vital in the lab glassware manufacturing process. These measures not only safeguard the quality and safety of the glassware but also reinforce the trust and confidence of users, making them indispensable in delivering reliable and high-standard laboratory glassware.

Continuous Improvement and Scientific Collaboration: Elevating Lab Glassware Standards
In the quest to achieve unparalleled quality in laboratory glassware, two additional pillars play a crucial role: continuous process improvement and collaboration with the scientific community. These aspects are key to not only meeting but also exceeding the evolving standards and expectations in scientific research.
10. Continuous Process Improvement: Driven by quality control data, customer feedback, and technological advancements, continuous improvement in manufacturing processes and quality control techniques is essential. This involves regularly updating and refining manufacturing methods to stay ahead of the ever-changing scientific requirements. Such continuous enhancements are crucial for elevating the quality of glassware, ensuring that each product not only meets but exceeds the stringent demands of scientific accuracy and reliability.
11. Collaboration with the Scientific Community: Engaging with the scientific community to gain feedback and insights is invaluable for quality improvement. Collaborations with research institutions, laboratories, and industry experts provide manufacturers with a deeper understanding of the changing needs of end-users. This collaboration helps in enhancing the design and functionality of the glassware, ensuring that it aligns with the latest scientific practices and discoveries. Such partnerships are instrumental in driving innovation and ensuring that the laboratory glassware remains relevant and effective in the face of scientific advancements.
The commitment to continuous process improvement and active collaboration with the scientific community are vital components in the manufacturing of laboratory glassware. These practices not only ensure that the glassware meets the current scientific standards but also anticipate future needs, thereby contributing to the ongoing advancement and reliability of scientific research. Through these efforts, manufacturers of laboratory glassware demonstrate their dedication to excellence and innovation in supporting the scientific community.
Conclusion
“Crafting Perfection” stands as a testament to the intricate and essential processes behind laboratory glassware manufacturing. It calls upon industry professionals, researchers, and students to acknowledge and appreciate the meticulous efforts that go into ensuring the precision and reliability of lab glassware. Let this article serve as an insightful guide and a call to action for continuous innovation and excellence in the field, pushing the boundaries of scientific discovery through superior quality control measures.