Have you ever marveled at the delicate and precise design of laboratory glassware? How are these essential tools of scientific discovery made? What skills and technologies are involved in crafting these glass instruments that are both resilient and accurate?
The creation of laboratory glassware is an art form that combines ancient techniques with modern technology. This intricate process ensures that scientists and researchers have reliable tools for their groundbreaking work. The craftsmanship behind each piece of laboratory glassware is a testament to the fusion of science and art.
Understanding the craft behind laboratory glassware keeps us connected to the roots of scientific discovery.

The Evolution of Glassware Manufacturing: From Ancient Techniques to Automated Solutions
Venturing into the world of chemistry labs, one encounters an array of intricate and precise glassware, essential for conducting myriad experiments. The journey of these glass pieces from raw materials to refined instruments is a tale of evolving technology and craftsmanship. Let’s delve into the fascinating manufacturing methods that transform simple glass into the vital tools of scientific discovery.
The manufacturing methods for glassware in chemical laboratories primarily include the following techniques:
- Hand Blowing Method: This is the earliest and simplest method for making glassware. Workers mix glass materials in specific proportions, heat them in a fire-resistant kiln, and then blow them into various shapes. This method relies heavily on manual labor, resulting in lower production efficiency and variable product quality.
- Mechanical Pressing Method: Here, the mixed glass materials are placed in a press machine, and the glass is shaped through mechanical pressing. This method can produce more uniform glassware at a higher efficiency. However, it requires large machinery, leading to higher costs.
- Mold Casting Method: In this method, the glass mixture is placed into a mold, which is then heated in a furnace. Once the molten glass fills the mold, it is cooled and solidified, and the glassware is formed upon demolding. This technique allows for the production of various shapes and sizes of glassware with high efficiency but requires expensive mold materials.
- Thermal Molding Method: This involves placing the glass mixture into a metal mold and then heating and pressurizing it to melt and shape the glass. This method can produce complex glassware designs with high efficiency but requires equipment capable of high temperatures and pressures, thus increasing the cost.
- Centrifugal Molding Method: The glass mixture is placed in a centrifuge, and through high-speed rotation, it is shaped into thin sheets. After heating and pressing, the glassware is formed. This method is efficient for producing thinner glassware but also requires large-scale machinery.
There are multiple methods for manufacturing glassware in chemical laboratories, each suitable for different production scales and product types. With ongoing technological advancements, new methods like 3D printing are emerging. These newer methods not only improve production efficiency but also enhance product quality and reduce costs. Moreover, with increasing demands for environmental protection and safety, some traditional methods are being phased out or improved. Future developments in technology are likely to lead to more intelligent, automated, and eco-friendly manufacturing processes for glassware.
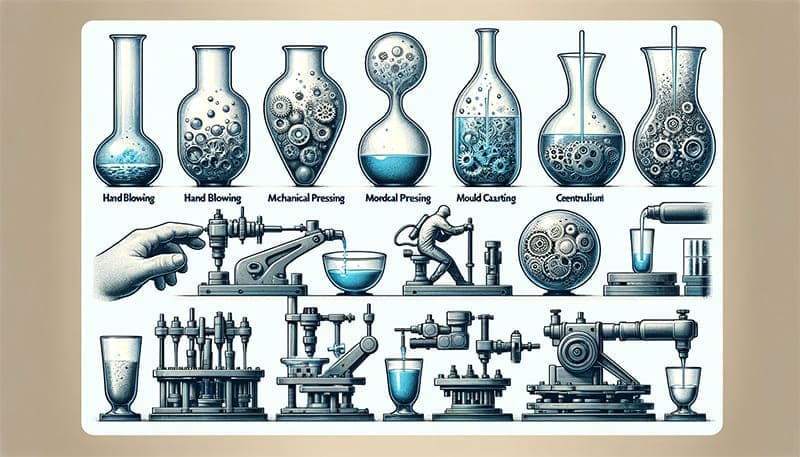
Comparative Analysis of Glassware Manufacturing Techniques
In the realm of laboratory glassware production, various techniques are employed, each with its unique strengths and limitations. To provide a clearer understanding, here’s a comparative table that outlines the key advantages and disadvantages of each manufacturing method, as well as the types of glassware products best suited for these techniques.
Manufacturing Method | Advantages | Disadvantages | Suitable Products |
Hand Blowing Method | – Customization and flexibility for unique designs – Artisanal quality | – Lower efficiency and higher time consumption – Variable quality due to reliance on manual skills | Custom and intricate glassware like specialized distillation columns, bespoke laboratory vessels |
Mechanical Pressing Method | – High uniformity, ideal for standard shapes – Suitable for mass production, scalable | – Limited design flexibility – Higher initial cost for machinery | Standard laboratory glassware like beakers, flasks, test tubes |
Mold Casting Method | – Versatile in producing a variety of shapes and sizes – Efficient for complex designs | – High initial cost for mold design and manufacture – Longer production time compared to mechanical pressing | Complex shapes like reaction vessels, custom flasks, and specialized lab equipment |
Thermal Molding Method | – Capable of producing intricate and detailed shapes – High efficiency for high-volume production | – Requires expensive high-temperature and high-pressure equipment – High energy consumption | Glassware with complex geometries and high precision requirements like precision lenses and specialized optical components |
Centrifugal Molding Method | – Excellent for producing thin-walled glassware – Ideal for cylindrical shapes and large-scale production | – Limited in producing complex or non-symmetrical designs – Requires large-scale machinery | Thin-walled and large-diameter glassware like large tubes and cylindrical containers |
Each of these five manufacturing methods for laboratory glassware – Hand Blowing, Mechanical Pressing, Mold Casting, Thermal Molding, and Centrifugal Molding – has its unique place in the spectrum of glassware production. From the artisanal quality of hand-blown glass to the precision and scalability of mechanical pressing and mold casting, each technique offers distinct benefits. Thermal molding and centrifugal molding further expand the range of possibilities, enabling the creation of complex and thin-walled glassware, respectively. Understanding these methods provides insight into the intricate processes behind the everyday scientific tools in laboratories, showcasing a blend of historical craftsmanship and modern technological innovation.
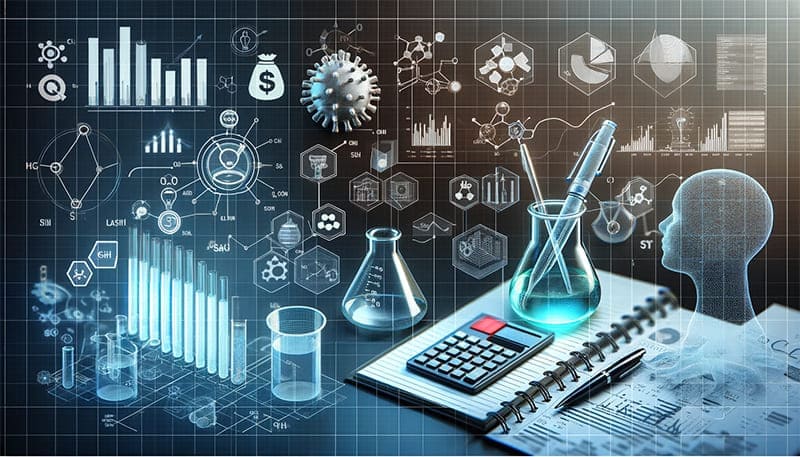
Economic Analysis of Laboratory Glassware Manufacturing Techniques
Economic considerations play a crucial role in the selection and application of the five different glassware manufacturing techniques. Each method varies not only in its technical aspects but also in its economic implications. Here’s an overview of how these factors influence the production of laboratory glassware:
Hand Blowing Method
- Cost Implications: Labor-intensive and time-consuming, this method incurs higher costs due to the skilled labor required. The uniqueness of each piece, however, can justify these costs in niche markets.
- Market Dynamics: The demand for hand-blown glassware is typically limited to specialized applications where customization and artisanal quality are valued over cost.
- Quality-Cost Balance: While offering high customization and quality, the hand blowing method may not be economically viable for standard laboratory glassware used in high volumes.
Mechanical Pressing Method
- Cost Implications: Initial investment in machinery is significant, but the method offers lower per-unit costs in mass production, making it economically efficient for large-scale manufacturing.
- Market Dynamics: This method aligns well with the market demand for standardized and bulk laboratory glassware, offering a balance of quality and affordability.
- Quality-Cost Balance: Mechanical pressing achieves a good balance by providing uniform quality at a relatively lower cost, suitable for widely used laboratory items.
Mold Casting Method
- Cost Implications: Mold casting involves substantial initial investment in mold design and manufacturing. However, it’s cost-effective for producing complex designs in large quantities.
- Market Dynamics: Ideal for markets requiring customized or complex glassware shapes, where customers are willing to pay a premium for specialized designs.
- Quality-Cost Balance: Offers a balance in scenarios where complex designs are required without compromising on the economies of scale.
Thermal Molding Method
- Cost Implications: The need for high-temperature and high-pressure equipment results in high capital and operational costs. However, its efficiency in producing complex items can offset these costs.
- Market Dynamics: Suitable for specialized markets that require high precision and complex designs, often found in advanced scientific research environments.
- Quality-Cost Balance: While expensive, it’s justified for producing high-precision and specialized glassware where quality and complexity are paramount.
Centrifugal Molding Method
- Cost Implications: Requires significant investment in centrifugal machinery. Economically viable for producing large volumes of thin-walled glassware.
- Market Dynamics: This method is aligned with the production of standard items like tubes and cylindrical containers, where the market demands high volume at lower costs.
- Quality-Cost Balance: Provides an economical solution for producing standard, thin-walled glassware in bulk, but less suitable for complex or low-volume items.
The economic aspects of these glassware manufacturing methods highlight a dynamic interplay between the costs of production, market demands, and the balance between quality and affordability. Each method finds its niche based on these factors, influencing the choice of technique for different types of laboratory glassware.
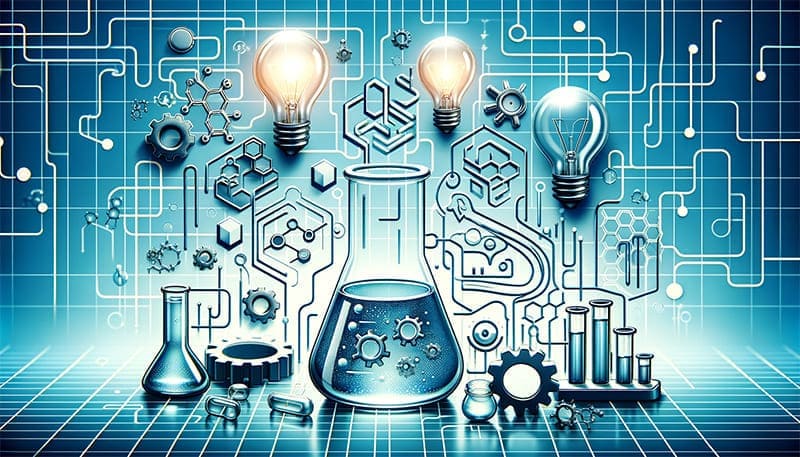
Navigating the Challenges and Opportunities in Laboratory Glassware Manufacturing: A Perspective on Production Techniques
The production of laboratory glassware encompasses various challenges and opportunities, shaped by its manufacturing techniques. Understanding these aspects is key to addressing the present difficulties and capitalizing on potential advancements in the field.
Challenges in Glassware Manufacturing
- Cost vs. Quality Trade-Off: Manufacturers often grapple with balancing the cost of production and maintaining high-quality standards. Techniques like hand blowing offer superior quality but at a higher cost, while methods like mechanical pressing are cost-effective but may not achieve the same level of craftsmanship.
- Technological Limitations: Each manufacturing method has limitations in terms of the complexity and precision of the glassware it can produce. Overcoming these limitations without escalating costs remains a significant challenge.
- Environmental Concerns: The glassware manufacturing process can be energy-intensive, especially methods like thermal molding. Reducing carbon footprint and managing waste are growing concerns, given the increasing focus on environmental sustainability.
- Adapting to Market Demands: The laboratory glassware market is evolving, with a growing demand for customized and specialized products. Adapting manufacturing processes to meet these changing needs, while remaining economically viable, is a constant challenge.
- Skilled Labor Shortage: Techniques like hand blowing require skilled artisans, and there’s a growing concern about the shortage of such skilled labor. Training and retaining craftsmen in an age where automation is predominant is a significant challenge.
Opportunities in Glassware Manufacturing
- Technological Innovation: Advancements in manufacturing technologies offer significant opportunities. Automation, AI, and robotics can increase efficiency and precision in glassware production, particularly in methods like mechanical pressing and mold casting.
- Sustainable Manufacturing: There’s a growing opportunity to adopt more sustainable manufacturing practices. This includes using recycled materials, reducing energy consumption, and implementing waste management strategies.
- Customization and Specialization: The demand for specialized glassware opens avenues for customized production, particularly in hand-blown and mold-casting techniques. This niche market could be lucrative and allow manufacturers to offer unique, high-value products.
- Emerging Markets and Applications: Expansion into new markets and applications, such as biotechnology and nanotechnology, provides opportunities for growth and innovation in glassware design and production.
- Collaboration with Academia and Research Institutions: Collaborating with research institutions for product development and testing can lead to innovations in glassware that better meet the evolving needs of the scientific community.
The manufacturing of laboratory glassware, while facing several challenges, also stands at the cusp of significant opportunities. Embracing technological advancements, focusing on sustainable practices, and adapting to market changes can help overcome these challenges and capitalize on the opportunities present in this evolving industry.
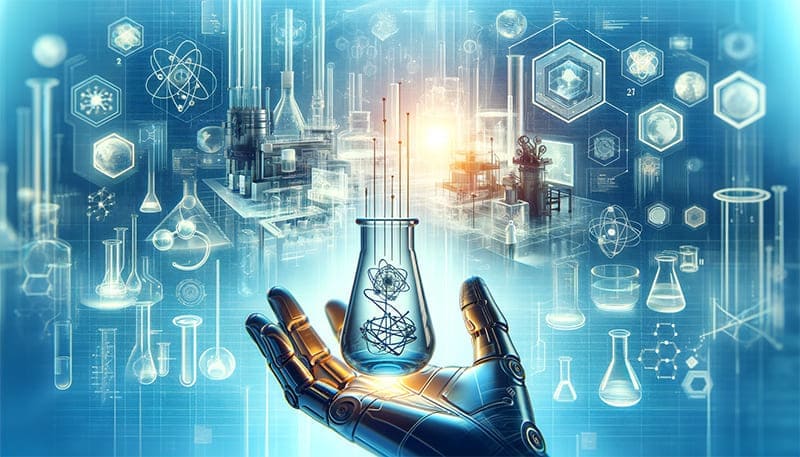
Conclusion
The journey of manufacturing laboratory glassware is a testament to human ingenuity and adaptability. From the ancient art of hand blowing to the precision of modern automated methods, each technique offers a unique contribution to the scientific world. While challenges such as balancing cost and quality, navigating technological limitations, and addressing environmental concerns pose significant hurdles, they also pave the way for innovative solutions and advancements.
As we embrace technological innovations, strive for sustainable practices, and adapt to the evolving needs of the scientific community, we open doors to new possibilities and advancements.