Have you ever wondered how crucial the role of glass instruments is in a laboratory? What are the implications of using instruments that aren’t up to standard? What kind of risks are we talking about here?
Ensuring the integrity and functionality of glass instruments is fundamental to maximizing lab efficiency and safety. This involves a range of performance tests – from appearance checks to temperature adaptability assessments – that ascertain their reliability under various conditions.
It’s essential to keep reading if you’re involved in laboratory work or are just curious about the science behind it.
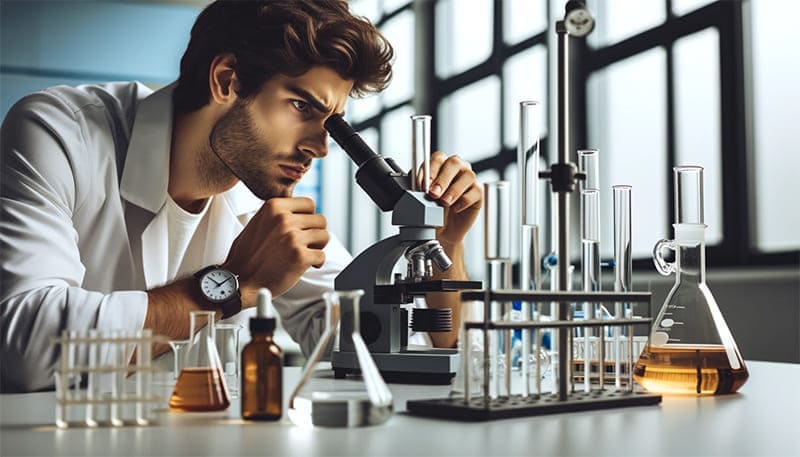
Why is Performance Testing Critical for Glass Instruments in Laboratories
Performance testing for glass instruments is not just a routine check but a cornerstone of laboratory safety and efficiency. Imagine conducting a high-stakes experiment, only to have it compromised by a faulty beaker or flask. The consequences can range from minor setbacks to catastrophic failures. Therefore, understanding and executing these tests effectively becomes a non-negotiable aspect of laboratory management.
The Benefits of Rigorous Performance Testing
By rigorously testing glass instruments, laboratories can:
- Ensure the safety of personnel and the environment.
- Guarantee the accuracy and reliability of experimental results.
- Extend the lifespan of glassware, thus saving costs.
- Uphold compliance with regulatory standards and quality assurance protocols.

The Essential Tests for Glass Instrument Performance
- Visual Inspection: Carefully observe the appearance of the glass instruments for any obvious defects, cracks, bubbles, or quality issues. Ensure the dimensions, shape, and markings meet design requirements.
- Pressure Resistance Test: Test the glass instrument’s pressure resistance by gradually applying or reducing pressure. Monitor for any deformation or breakage to assess the reliability and safety of the glass instrument under high or vacuum pressures.
- Impact Resistance Test: Simulate real-life impact scenarios to test how the glass instrument withstands shocks. Apply a specific impact force and observe for any cracks or breakage. This test evaluates the instrument’s resistance to accidental impacts during use.
- Seal Test: Check the sealing performance by detecting gas leaks under pressurized or depressurized conditions. Place the glass instrument in a sealed container and gradually alter the pressure to observe any gas leakage. This test assesses the gas sealing performance to prevent safety hazards from gas leaks.
- Corrosion Resistance Test: Immerse the glass instruments in corrosive solutions or expose them to corrosive environments to evaluate their resistance to chemicals. Regularly check for surface corrosion and record data to assess the instrument’s resistance to chemicals, extending its lifespan and safety.
- Transparency Test: Test the transparency of the glass instrument to ensure clear observation of internal changes during use. Place the instrument under a light source and observe for any impediments like bubbles or impurities. This test ensures accuracy and reliability in experimental results.
- Temperature Adaptability Test: Subject the glass instrument to different temperature environments by heating or cooling to test its adaptability to temperature changes. Gradually change the temperature and observe for cracks or breakage. This test assesses the instrument’s resistance to temperature changes, ensuring accurate and reliable experimental results.
- Reliability Test: Simulate long-term usage scenarios to test the glass instrument’s reliability and stability. Use the instrument over an extended period and monitor its performance and changes. This test evaluates the stability and durability of the glass instrument during use, ensuring accurate and reliable experimental outcomes.
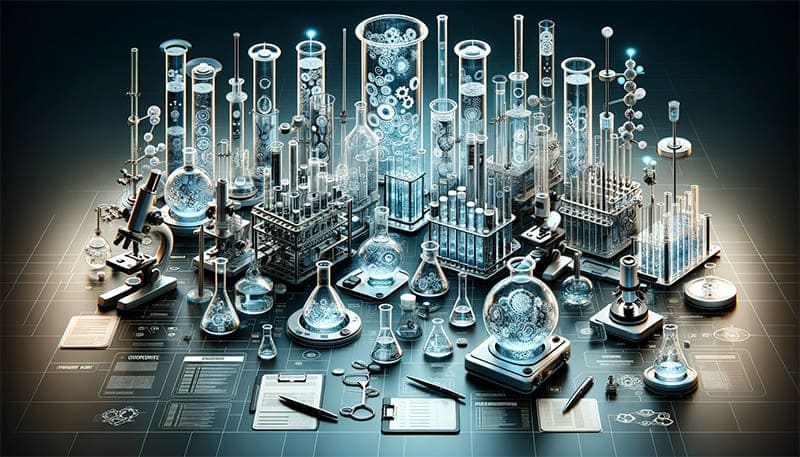
Comprehensive Performance Testing of Glass Instruments
To ensure the highest standards of quality and safety, glass instruments must undergo a series of rigorous performance tests. Each test targets specific potential flaws and operational challenges, providing insights into the instrument’s reliability and durability in practical scenarios. Below is a detailed examination of the eight critical testing methods, highlighting the flaws to look for and the essential considerations for each test.
Testing Method | Primary Flaws to Look For | Key Considerations |
---|---|---|
Visual Inspection | Cracks, bubbles, defects | Ensure conformity to design specs; check thoroughly |
Pressure Resistance Test | Deformation, breakage | Gradually apply/reduce pressure; monitor closely |
Impact Resistance Test | Cracks, breakage | Apply controlled impact; observe for damage |
Seal Test | Gas leaks | Test in sealed conditions; monitor for leaks |
Corrosion Resistance Test | Surface corrosion | Immerse in corrosive environment; record changes |
Transparency Test | Bubbles, impurities | Ensure clear visibility; test under light |
Temperature Adaptability Test | Cracks, breakage due to temperature changes | Test across temperature ranges; monitor structural integrity |
Reliability Test | Performance degradation | Long-term use simulation; monitor for stability |
Method Details and Considerations:
- Visual Inspection: Look for any irregularities in the material or construction. Consider using magnification tools for small imperfections and ensure the instrument is clean for accurate inspection.
- Pressure Resistance Test: It’s important to increase pressure incrementally to identify at what point, if any, the glass begins to deform or break. Safety measures should be in place to handle sudden breakage.
- Impact Resistance Test: The type and magnitude of impact should simulate realistic conditions. It’s crucial to ensure the test doesn’t overly weaken the structure for subsequent uses.
- Seal Test: The test should mimic the operational pressure conditions of the glassware. Ensure that seals and joints are checked with appropriate pressure or vacuum conditions.
- Corrosion Resistance Test: The selection of corrosive agents should reflect the actual chemicals the glassware will be exposed to. Post-exposure, the glassware needs thorough examination for subtle changes.
- Transparency Test: Lighting conditions should be consistent and representative of typical use cases. Any abnormalities in transparency could affect measurements or observations in actual use.
- Temperature Adaptability Test: The range of temperature fluctuations should cover the expected operational extremes. Sudden temperature changes might be more damaging than gradual ones, so consider the rate of change.
- Reliability Test: This involves a long-term assessment, often under the conditions of regular use. It’s crucial to simulate as closely as possible the actual stress and wear the glassware will encounter.
By following these methods and considerations, you can ensure comprehensive performance testing of glass instruments, covering all critical aspects of functionality and durability.
How to Conduct These Tests Effectively?
Conducting these tests requires a blend of technical know-how and practical skills. Here are some key points to consider:
- Use calibrated equipment for testing to ensure accurate results.
- Document each test meticulously for future reference and compliance purposes.
- Train laboratory personnel on the significance and methods of these tests.
- Regularly review and update testing protocols to align with the latest safety standards.

Error and Risk Management in Laboratory Settings
Performance testing of glass instruments is a crucial component of the broader error and risk management strategies in laboratory settings. Effective testing helps mitigate a variety of risks and errors, ensuring the safety of personnel, the integrity of the experiments, and the reliability of the results. Here are some specific errors and risks that performance testing addresses:
- Cross-Contamination: Inadequate or damaged glassware can lead to cross-contamination between samples. Performance testing ensures that glass instruments are intact and free from cracks or fissures that might harbor contaminants. Regular checks for chemical residues and the integrity of the glass can prevent cross-contamination, which could otherwise lead to erroneous results or unsafe conditions.
- Exposure to Toxic Substances: Cracked or poorly functioning glassware can leak, leading to exposure to toxic chemicals or biological agents. Performance testing, particularly seal and pressure tests, ensures that containers are secure and can safely hold or transport hazardous materials without risk of exposure.
- Inaccurate Experimental Results: Flaws in glass instruments can introduce errors into experimental results. For instance, a small crack in a measuring device could lead to incorrect volume measurements. Performance testing ensures the accuracy and precision of instruments, which is critical for maintaining the validity of experimental outcomes.
- Physical Injuries: Broken glassware is a common lab accident that can lead to severe injuries. Regular performance testing helps identify weakened or damaged glassware before it breaks, thereby reducing the risk of cuts and other injuries.
- Chemical Reactions and Explosions: Certain chemical reactions require glassware to withstand high pressures or temperatures. If a piece of glassware is not up to standard, it might crack or explode, leading to potentially dangerous reactions. Temperature adaptability and pressure resistance tests are essential to prevent such incidents.
- Equipment and Experiment Costs: The failure of glass instruments can lead to costly equipment damage and the need to repeat expensive experiments. Performance testing helps ensure that glassware is reliable and can withstand the rigors of experimental procedures, saving time and resources in the long run.
- Regulatory Compliance Risks: Laboratories are often subject to strict regulatory requirements regarding safety and accuracy. Failure to adequately test and maintain equipment can lead to non-compliance, resulting in fines, legal issues, or the revocation of licenses.
- Reputation Damage: Incidents resulting from failed glassware can damage a laboratory’s reputation. Rigorous performance testing helps maintain a standard of excellence and trust, which is crucial for attracting research funding, partnerships, and top talent.
By integrating comprehensive performance testing into their error and risk management strategies, laboratories can significantly reduce these risks and errors, leading to safer, more efficient, and more reliable operations. It’s not just about preventing negative outcomes but also about promoting a culture of quality and safety that pervades every aspect of the laboratory’s work.

Enhancing Lab Competency: Training and Education for Performance Testing
Training and Education for Lab Personnel: To effectively conduct performance testing of glass instruments, laboratory personnel must possess a specific set of skills and knowledge. This typically involves a combination of formal education, hands-on training, and continuous learning. Here are key components of the training and education necessary for lab personnel:
- Formal Education: A foundational understanding of chemistry, biology, physics, or a related scientific field is crucial. This provides the theoretical background necessary to understand the properties of glass, the nature of chemicals, and the principles behind various laboratory techniques.
- Technical Training: Personnel should receive specific training on the types of glass instruments used in their lab, understanding their limitations, and the correct methods for performing performance tests. This often includes instructions on handling equipment, conducting tests like pressure or temperature resistance, and interpreting results.
- Safety Training: Given the risks associated with handling glassware and chemicals, safety training is essential. This includes proper handling techniques, understanding of material safety data sheets (MSDS), emergency procedures, and personal protective equipment (PPE) usage.
- Quality Assurance and Regulatory Training: Staff should be familiar with the quality standards and regulatory requirements relevant to their work. This includes training on standard operating procedures (SOPs), documentation practices, and understanding of compliance matters related to laboratory testing and safety.
- Ongoing Education and Updates: The field of laboratory science is continually evolving, with new techniques, materials, and regulations emerging regularly. Laboratories should therefore provide opportunities for ongoing education, whether through workshops, seminars, online courses, or attendance at conferences. This ensures that personnel are up-to-date with the latest developments in performance testing and laboratory best practices.
By investing in comprehensive training and continuous education for laboratory personnel, institutions can maintain high standards of safety, accuracy, and efficiency in their use of glass instruments. This not only protects the integrity of the work conducted but also enhances the reputation and effectiveness of the laboratory as a whole.

Balancing Expenditure and Efficiency: Cost-Benefit Analysis of Performance Testing
Investing in performance testing for glass instruments in laboratories is not just a safety measure but also a strategic financial decision. Understanding the cost-benefit analysis helps justify the allocation of resources towards regular testing. Here’s a breakdown of the major considerations:
- Initial Investment: Includes the cost of testing equipment, training, and time. Modern testing techniques, however, can offset these with efficiency and longevity.
- Avoiding Equipment Failures: Early detection through testing prevents costly replacements and repairs, extending the life of glassware.
- Reducing Experimental Errors: Inaccurate results lead to repeated experiments. Consistent testing ensures reliability and saves the cost of redoing work.
- Preventing Hazards: Safety breaches from faulty equipment can lead to expensive accidents. Regular testing mitigates these risks.
- Long-Term Benefits: A sound testing regimen enhances a lab’s reputation, ensures consistent results, and can lead to more efficient research outcomes.
The upfront costs of performance testing are far outweighed by the safety, accuracy, and cost savings it ensures, making it a wise investment for any laboratory.
Conclusion
In mastering the art and science of performance testing, your lab isn’t just committing to regulatory compliance; it’s championing the cause of unwavering accuracy, steadfast safety, and unrivaled efficiency. Embrace these practices not as a mere obligation but as a beacon of excellence in scientific pursuit. Dive into the world of performance testing, and let each test be a step towards groundbreaking discoveries and innovation. Your commitment to quality today defines the successes of tomorrow.